by using Prism
BIM project
produced offsite
Investment in biopharmaceuticals is critical to the future of pharmaceuticals and for that reason, science-led global healthcare company GSK, committed £94m to designing and constructing an 11,500 sq m highly complex and world-leading, state-of-the-art, aseptic manufacturing facility – Q Block at its Barnard Castle site, in County Durham and chose the best in digital and offsite construction as the preferred methods to deliver the project.
As can be expected of a pharmaceutical manufacturer, GSK works to the highest standards. These exacting standards and the need to guarantee quality and maintain tight control over the build process and schedule, along with the manufacturer’s desire to be able to replicate the building anywhere in the world, were key drivers in choosing offsite as the central construction method and which led to SES’ direct appointment with GSK.
The early appointment of the project team, particularly SES, ensured that offsite manufacturing principles, prefabrication and BIM could be applied to best effect. This was particularly the case in relation to SES when the contractor’s BIM Level 2 expertise and experience combined with Prism; its bespoke offsite manufacturing facility, ensured that the contractor was able to influence the M&E design at the outset of the complex and highly regulated facility.
BIM technology and its uses grew on GSK throughout this project. It initially only required clash control and engineering enabled BIM use, to looking at how BIM can improve facilities management and business readiness. Although Augmented Reality had only just started to be used at Barnard Castle, examples of its success can now be seen on site and the team is planning on further exploring its uses.
SES worked to a detailed schedule of works to install all mechanical and electrical (M&E) building services, ensuring that there was minimum disruption to the live manufacturing site which completed in January 2020.
Colin Driver, Project Manager, GSK said:
“The investment in biopharmaceuticals is critical to the future of pharmaceuticals and this is a flagship project for global investment. The idea is to replicate the design globally on secondary sites, building in the flexibility within individual modules, but also future-proofing the design for at least 10-20 years without the risk of drug regulatory impact, hence reducing future design costs. I believe this can only be achieved using offsite technology.”
Other Case Studies
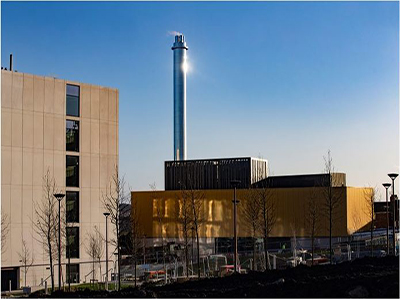
Newcastle District Energy Centre
Supporting the city of Newcastle Upon Tyne in its endeavours to go carbon neutral by 2030, SES Engineering Services (SES) was directly appointed by Engie as main contractor to design and install complex MEP solutions on Newcastle District Energy Centre.
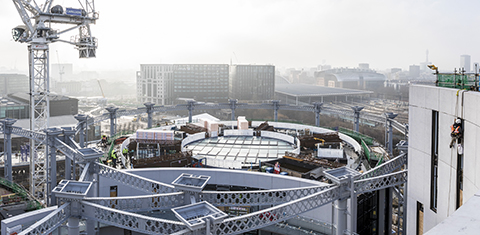
Gasholders London
Set in King’s Cross – one of the largest areas of central London to be developed in the last 150 years – the circular Gasholders London project is a pioneering example of cutting-edge offsite manufacturing and prefabrication.
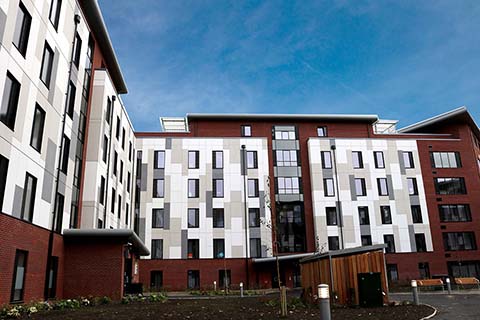
University of Hull
As the student accommodation sector continues to be a source of new work for leading national engineering specialist SES Engineering Services (SES) who were appointed by main contractors Sewell Construction completed a £6.5m contract at the University of Hull.