taken offsite
days of work
products installed
development
At the heart of the Norwich Research Park, the contemporary and purpose-designed Quadram Institute will house research teams from the Institute of Food Research, the University of East Anglia, as well as the Norfolk and Norwich University Hospitals NHS Foundation Trust.
SES Engineering Services (SES) was brought on board at the design phase – a decision that impacted all stakeholders and ensured a smooth project sequence and truly minimised clashes. Full utilisation of BIM enabled SES to work with the MEP design team to maximise the offsite strategy.
With this clear strategy, SES executed its offsite approach during the pre-construction period to not only match the initial bid target for offsite manufacture but to exceed this with the development of risers, plantrooms and service modules to be delivered by SES’ offsite manufacturing facility, Prism. To achieve this success, the SES team embraced a true collaboration and ‘one team’ ethos with its key project partners.
From start to finish, the outstanding level of trust, transparency and collaborative decision-making spearheaded by SES – on what was a £19m M&E contract for the business – has not only produced unprecedented project outcomes and savings but also ensured the project met strict programme requirements.
The building’s scale and the logistical challenges of a confined site would have made producing modules on site extremely difficult and therefore offsite was the only sensible option from day one. The use of offsite manufacturing resulted in over 8,000 man hours taken from site, and also saved roughly 1,000 days, resulting in a huge benefit to the client.
In total, SES delivered 36 plantroom prefabricated AHU valve arrangements, four plantroom pump skids and 164 pipework and electrical containment modules. In addition, six ductwork risers, four pipework risers and three electrical risers were installed each complete with platforms four floors in height.
This project has been delivered with offsite methodology at its core and, critically, the project sequence would have been far more challenging without it.
Dr Nick Goodwin, Programme Manager, BBSRC commented:
“It has been a hugely refreshing experience to work with design, construction and engineering contractors who share such a clear and transparent attitude to collaboration.
“The engineering complexity of combining research and healthcare provision under one roof created many unique challenges for both the client and contractor. Right at the architectural design stage, a commitment to quality and detailed design achieved through offsite manufacturing was of a level we’ve not seen before and we’ve been hugely impressed.”
Other Case Studies
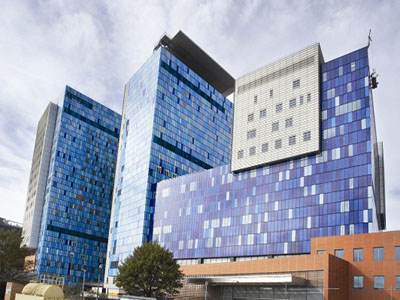
Royal London Hospital
In less than five weeks, SES Engineering Services (SES) and Wates Construction delivered a full fit-out of floors 14 and 15 at Royal London Hospital, to create additional capacity for more than 170 intensive care beds to support the COVID-19 pandemic.
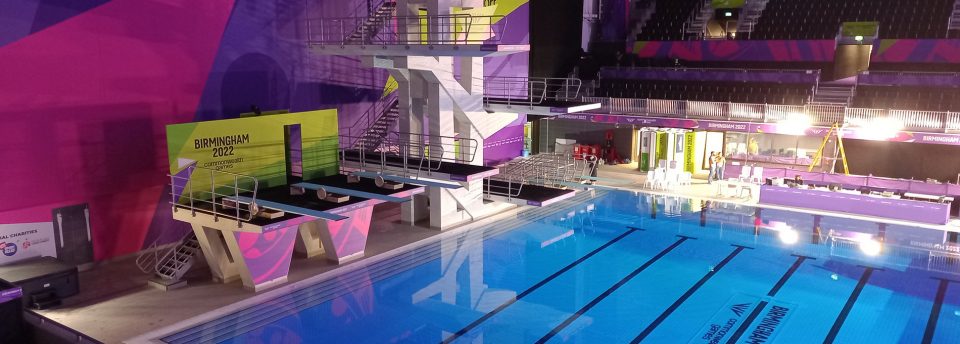
Sandwell Aquatics Centre
The Sandwell Aquatics Centre was initially constructed to host one of the most significant international sporting events of 2022
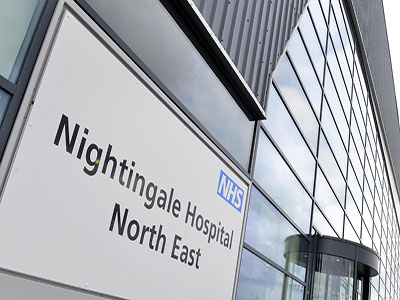
Nightingale Hospital North East
Leading national engineering specialist, SES Engineering Services (SES) has supported the fight against the coronavirus recently supporting with the installation of mechanical and electrical (M&E) services at the new 460-bed NHS Nightingale Hospital North East in Sunderland.